ÁREA
Química de Materiais
Autores
Francisco, T. (INT/UFRJ) ; Oliveira, F. (INT/IME) ; Eufrazio, E. (INT/UFF) ; Moreira, R. (INT/INMETRO) ; Souza, D. (UFRJ)
RESUMO
Atualmente, a busca por opções mais sustentáveis está em alta. Uma abordagem promissora é usar fibras naturais em compósitos de poliuretano para substituir o poliestireno expandido. A absorção de impacto, importante em embalagens, automóveis e capacetes, é um atributo que pode melhorar. Este estudo visa avaliar a absorção de impacto de compósitos de poliuretano com fibras de coco, sisal e bagaço de cana em diferentes proporções. Os resultados mostram bom desempenho na absorção de impacto com 5% e 10% de fibras de coco, além de 10% de fibras de sisal. Isso impulsiona o desenvolvimento de materiais sustentáveis mais resistentes, atendendo às necessidades de vários setores industriais.
Palavras Chaves
Poliuretano; fibras naturais; Absorção de Impacto
Introdução
O desenvolvimento de materiais mais sustentáveis, ambientalmente amigos tem-se tornado um apelo crescente mundial. De acordo com as Organização das Nações Unidas (ONU) um dos objetivos de desenvolvimento sustentável é a proteção do meio ambiente e do clima. Neste sentido os compósitos de poliuretanos com fibras naturais têm demonstrado ser uma opção ao uso do poliestireno expandido. O poliestireno é formado por monômeros de estireno que derivados do benzeno, obtidos pela extração de petróleo, e são altamente reativos. Possuem degradação lenta, baixa taxa de reciclagem e durante a síntese do polímero, liberam vapores orgânicos tóxicos que podem apresentar risco a saúde e ao meio ambiente. O poliuretano é um material versátil e possui propriedades mecânicas que se assemelham ou são melhores as do EPS. Além disso, as formas de reciclagem do poliuretano são mais eficientes que as do EPS, além de poder ser reutilizado. (AKINDOYO, John Olabode et al,2016 ; DAS, Arpan et al, 2020;ZIA, Khalid Mahmood, et al.,2007). A síntese do poliuretano ocorre por poliadição entre o grupo isocianato e as hidroxilas do poliol, formando assim ligações uretano (ZIA, Khalid Mahmood, et al.,2007). A escolha dos materiais para a síntese pode tornar o poliuretano mais ou menos poluente. Geralmente, a síntese é realizada por isocianatos, sendo o MDI (diisocianato de difenilmetano) e o TDI (diisociato de tolueno) os mais comuns, juntamente com o poliol. O TDI é obtido por síntese a partir do tolueno, que é derivado do petróleo, enquanto o MDI é produzido pela obtido a partir da reação da anilina com formaldeído formando o a 4,4-metileno-bis(fenilisocianato). Contudo, os polióis podem ser derivados do petróleo ou ter, origem vegetal, como a glicerina. Além disso, trabalhos na literatura mencionam o uso de óleo de soja, óleo de milho, mamona, entre outros. Outro fator que contribui para a característica ambientalmente amigável do poliuretano é a possibilidade de extrair pólios ao reciclar o material (SINGH, Indresh et al.,2020; FIÉVET, Fernand;BRAYNER, Roberta.2012, TANAKA, Ryohei; HIROSE, Shuji; HATAKEYAMA, Hiroshi,2008). O poliuretano pode ser fabricado de duas maneiras por meio das sínteses “One shot” e “Two Steps”. A primeira envolve a mistura de todos os componentes em uma única etapa: polióis, isocianatos, agentes de expansão e aditivos, o que proporciona algumas vantagens como redução de tempo e ausência de pré- polimerização, tornando-o mais econômico. No entanto, esse processo deve ser utilizado para espumas flexíveis e termoplásticos (AKINDOYO, John Olabode et al ,2016;DAS, Arpan et al,2020 ;ZIA, Khalid Mahmood,2007). Já a síntese “Two Steps” é realizada em duas etapas distintas: na primeira etapa, ocorre a formação de um pré- polímero onde a proporção do isocianato é inferior ao desejado, resultando em ligações de uretano parciais, controladas pela adição de isocianato e temperatura da reação. Após essa etapa, ocorre a conclusão da reação, onde o complemento do isocianato é adicionado, completando assim as ligações uretano e formando assim o polímero. Na última, etapa agentes de expansão e aditivos são adicionados quando necessários (AKINDOYO, John Olabode et al,2016 ;DAS, Arpan et al,2020 ;ZIA, Khalid Mahmood,2007). Neste sentido, as fibras naturais são conhecidas, apesar de carga inerte, por suas propriedades mecânicas, como alta resistência e rigidez, além de sua capacidade de absorção de energia. A adição dessas fibras às espumas de poliuretano pode resultar em resultados interessantes para indústria de embalagens, automobilística de capacetes entre outras, devido ao melhoramento na resistência ao impacto (ATIQAH, A. et al.,2017.) Nesse contexto, o objetivo deste trabalho é avaliar o comportamento das fibras de coco, sisal e bagaço de cana nos compósitos à base de poliuretano, visando aprimorar a absorção de impacto. Essas fibras foram escolhidas devido à abundância de resíduos agroindústrias e ao fato de cultivos nacionais. Além disso, o coco possui uma resistência a tração entre 70 e 106 MPa, um módulo de elasticidade entre 3.0 e 6.0 GPa e um alongamento de ruptura entre 15.0 e 47.0%. Já o sisal possui uma resistência a tração entre 55.0 e 468.0 MPa, modulo de elasticidade entre 9.0 e 28.0 GPa e alongamento de ruptura entre 1.9 e 4.5 % (GIRALDELLI, Mariana Aparecida et al, 2020).
Material e métodos
Materiais e reagentes Poliuretano marca AVIPOL ®, tubo PVC de 100 mm, folhas de acetato, termômetro, máquina para ensaios de impacto vertical da marca AD ENGINEERING, modelo MAU 1006, composto de um sistema computacional que projeta os resultados dos ensaios, o free fall (g) e o tempo limite de impacto, cabeça de ensaio de 62 cm, água destilada, becker, bastão de vidro, Extran ® e tinner. As fibras de coco, sisal foram compradas no comercio local e o bagaço de cana foi cedido por feirantes locais. Estas foram tratadas com hidróxido de sódio PA (VETEC ®). Além disso, são necessários papel indicador, peneira de 1.0 mm, folhas de acetato e um agitador magnético. Metodologia: As fibras passaram por tratamento alcalino que consistiu em imergi-las em uma solução de hidróxido de sódio a 10%, por 15 minutos sob agitação de 1300 rpm. Após esta etapa, as fibras foram são lavadas com água destilada até atingirem o pH= 7 e, posteriormente, foram secas em uma estufa a 70 °C por um período de 24 horas. Em seguida, Após, as fibras foram cortadas e selecionadas por uma peneira de 1.0 mm. Para a produção dos protótipos de poliuretano cortou-se o tubo PVC em frações contendo uma altura aproximada de 10 mm, e em seguida, logo após foram lavados com Extran ® e água destilada. A produção da espuma ocorreu manualmente, misturando o poliol de poliéster (parte A) com 0%, 5%, 10%, 15%, 20% e 30% m/m de poliol de cada fibra. Logo em seguida, a massa de isocianato foi adicionada na proporção de 1:1 em relação ao poliol, conforme orientação do fabricante. A massa do compósito foi vertida nas frações de tudo PVC, seladas na parte inferior com folhas de acetato, e curadas por 48 horas, também seguindo a recomendação do fabricante. Os experimentos foram realizados em temperatura ambiente de 25 °C ± 5 °C. As fibras foram analisadas através de microscópio óptico para avaliar a eficiência do tratamento térmico e, após a cura, os compósitos foram testados quanto a absorção de impacto no Laboratório de Ensaio em Produtos (LAENP) do Instituto Nacional de Tecnologia (INT). Para uma avaliação mais precisa dos dados, foram produzidos 10 protótipos de cada tipo de fibra em cada porcentagem. O procedimento do teste de impacto baseou-se na norma ABNT NBR 7471:2015, que estabelece limites para a aceleração máxima permitida, visando a segurança do usuário. Esses limites consistem em não exceder 300 g em nenhum momento e evitar ultrapassar 150 g por um período superior a 5 ms. A aceleração máxima é expressa em múltiplos de g, sendo 1 free fall (g) = 9,80665 m/s². O ensaio é realizado com o uso da cabeça de teste com circunferência de 62 cm. A avaliação foi conduzida a partir de uma altura padrão, usualmente empregada em comparações interlaboratoriais, correspondente à queda de 50 centímetros (cm) de altura, iniciando-se a partir do ponto P da cabeça de ensaio, com uma velocidade inalterada de 3,13 ms.
Resultado e discussão
O tratamento alcalino das fibras visa eliminar a hemicelulose e a lignina
presentes nas mesmas. Esses polissacarídeos muitas vezes são incompatíveis com
os solventes utilizados nos polímeros. No caso do poliuretano, a hemicelulose e
a lignina são compostas hidrofílicos, enquanto o isocianato é um composto
hidrofóbico, dificultando a emulsão entre o poliol e o mesmo. Além disso, devido
à natureza hidrofílica, esses polissacarídeos podem absorver umidade do ar,
alterando a composição e a estrutura do compósito (Kuranchie, C., et al, 2021).
A lignina pode tornar o polímero mais frágil, uma vez que é um componente rígido
e inflexível podendo assim alterar a flexibilidade, uma propriedade essencial
nos elastômeros, além de alterar a resistência. A lignina e a hemicelulose podem
formar áreas fibrosas que podem se tornar sítios de concentração de tensão,
levando a falhas mecânicas no compósito especialmente nos ensaios de absorção de
impacto.(Kuranchie, C., et al , 2021).
Além disso, a lignina e a hemicelulose possuem uma alta temperatura para
degradação térmica o que pode afetar a Tg (temperatura de transição vitrea) e Tm
(temperatura de fusão) dos polímeros. A lignina por ser um composto amorfo e
rígido, pode interagir com a matriz polimérica e restringir a mobilidade
molecular, resultando no aumento da transição vítrea. Nesse caso, o polímero
fica mais rígido (Kim, S.,et al, 2015;El-Shekeil, Y. A., et al,2012) Por outro
lado, a hemicelulose, sendo um composto amorfo e flexível, terá o efeito oposto
ao da lignina.
Ambos os compostos podem afetar a temperatura de fusão e, consequentemente, a
cristalização dos polímeros, podendo alterá-la de tal forma que o polímero fique
mais rígido (Kim, S., 2015; El-Shekeil, Y. A., et al,2012)
A figura abaixo (figura 1) mostra como as fibras ficaram antes e depois do
tratamento.
A figura 1 representa a imagem das fibras no microscópio óptico aumento de 50
vezes e escala de 200 µm, (A) bagaço de cana antes do tratamento alcalino, (B)
bagaço de cana depois do tratamento alcalino, (C) fibra de sisal antes do
tratamento alcalino, (D) fibra de sisal depois do tratamento alcalino, (E) fibra
de coco antes do tratamento alcalino, (F) fibra de coco depois do tratamento
alcalino.
Observa-se pelas imagens do microscópio óptico que, no caso da fibra de bagaço
de cana (figura 1A e 1B), os cristais foram eliminados após a limpeza alcalina.
Nas fibras de sisal (figura 1C e 1D), nota-se uma diferença de coloração nas
fibras. Nas fibras de coco (figura 1E e 1F), percebe-se uma variação nas manchas
escuras e no diâmetro das fibras. Embora não seja possível confirmar totalmente
a remoção das camadas de lignina e hemicelulose por meio do microscópio óptico,
pode-se inferir que o tratamento alcalino teve algum impacto nas alterações
observadas nas fibras tratadas em relação às não tratadas.
É importante ressaltar que o tratamento químico dado às fibras visa melhorar a
adesão destas ao polímero, reduzir a hidrofilicidade, aumentar a durabilidade,
diminuindo a degradação interface-polímero ao longo do tempo e melhorando a
resistência à umidade e a gentes ambientais.
Durante a preparação dos compósitos, três fatores críticos foram identificados:
temperatura ambiente, a concentração das fibras e o comprimento das fibras. A
temperatura foi crucial para o procedimento devido ao tempo de manuseio da
espuma, uma vez que o tempo de gel do poliuretano utilizado foi de cerca de 30 s
a 25 °C. No entanto, ao tentar realizar a mesma produção na temperatura 40 °C o
tempo de gel diminuiu, dificultando o processo manual do poliuretano.
O comprimento das fibras foi o segundo fator a ser estudado, pois foi observado
que quanto maior o comprimento das fibras maior a cinética de expansão da
espuma. Portanto optou-se pela peneira de 1.0 mm, que se aproximava do
comprimento limite das fibras.
A concentração das fibras revelou-se um fator determinante para a estabilidade
da espuma. Compostos contendo 20% e 30% de fibras apresentaram baixa
estabilidade, com a espuma se desintegrando em partículas finas de espuma e
fibra. Assim, os testes subsequentes foram realizados apenas com compósitos
contendo entre 0% e 15% de fibras.
Para avaliação do comportamento dos compósitos em relação absorção de impacto os
valores registrados no ensaio de impacto foram submetidos a testes de
normalidade e outliers e com estes tratamentos obteve o gráfico abaixo (figura
2).
O gráfico acima representa as medias com seus desvio-padrão dos resultados do
ensaio de impacto já retirados os outliers.
Observa-se que, apesar das fibras naturais serem consideradas cargas inertes, à
adição das fibras como reforço tem o potencial de significativamente aprimorar a
absorção de impacto em comparação com o poliuretano não modificado. A figura
apresentada acima (Figura 2) mostra claramente que todos os compósitos
localizados abaixo da linha tracejada demonstram melhorias na absorção de
impacto em relação ao poliuretano puro. No entanto, alguns compósitos acima
dessa linha ainda se intersectam com o poliuretano puro, provavelmente devido às
variações presentes nos resultados das análises. Esses pontos de interseção não
indicam limitações, mas sim evidências de que, a inclusão das fibras naturais
favorece positivamente aprimoramentos nas propriedades de absorção de impacto.
Destaca-se a composição com 10% de fibras de sisal, caracterizada não apenas
pelo menor desvio-padrão, mas também por exibir valores reduzidos nos testes de
impacto. Também merece menção os compósitos contendo 15% de fibras de sisal, que
embora apresentem resultados de impacto ligeiramente superiores aos compósitos
com 10%, mantêm um desvio-padrão notavelmente baixo. Adicionalmente, merecem
atenção os compósitos com 5% de fibras de coco, evidenciando baixos valores nos
ensaios de impacto. Além disso, os compósitos constituídos por 10% de fibras de
coco e uma combinação de 5% de bagaço de cana também se destacam por suas
propriedades impactantes. Esses resultados realçam as possibilidades promissoras
dessas composições no aprimoramento de propriedades mecânicas e ressalvam sua
relevância no desenvolvimento de materiais resistentes e sustentáveis.
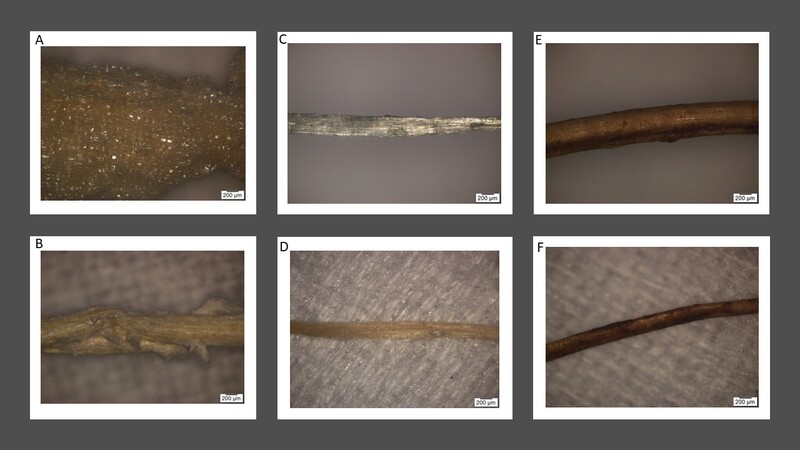
Figura 1:(A e B) bagaço de cana antes (C e D) fibra \r\nde sisal com tratamento, (E e F) fibra de coco
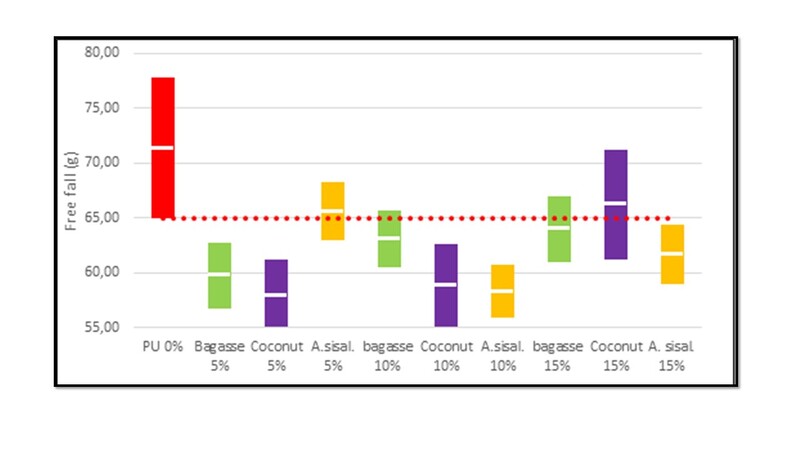
: Resultado do ensaio de Absorção de Impacto nos \r\ncompósitos a base de poliuretano
Conclusões
Com base nos resultados alcançados, torna-se cada vez mais evidente que a incorporação de fibras naturais representa uma solução econômica e altamente eficiente para otimizar a capacidade de absorção de impacto. Assim, apesar de serem originalmente consideradas como componentes inertes, as fibras naturais têm se firmado como cargas de reforço altamente eficazes para aprimorar a absorção de impacto. No âmbito ambiental, essa abordagem revela uma perspectiva promissora, pois a utilização mais abrangente de fibras naturais pode contribuir significativamente para a redução do resíduo orgânico depositado no meio ambiente. Alinhando-se a princípios de economia circular (ESG), essa abordagem oferece vantagens adicionais em termos industriais, promovendo a adoção de concentrações mais elevadas de fibras naturais. Até o presente momento, este estudo demonstrou ser viável e promissor. Para as próximas etapas, está prevista uma investigação mais aprofundada das características granulométricas das fibras, bem como a exploração de novos aditivos e estudos químicos e mecânicos mais detalhados. Essas ações prospectivas não apenas aprimorarão nosso entendimento das propriedades envolvidas, mas também ampliarão o escopo de aplicações e o potencial dessa abordagem inovadora.
Agradecimentos
The authors would like to thank the CAPES, Brazil, as well as the Brazilian agency CNPq for providing a scholarship, and MCTI, FAPERJ and FINEP for their significant assistance
Referências
AKINDOYO, John Olabode et al. Polyurethane types, synthesis and applications–a review. RSC Advances, v. 6, n. 115, p. 114453-114482, 2016.
ATIQAH, A. et al. A review on polyurethane and its polymer composites. Current Organic Synthesis, v. 14, n. 2, p. 233-248, 2017.
DAS, Arpan et al. A brief discussion on advances in polyurethane applications. Advanced Industrial and Engineering Polymer Research, v. 3, n. 3, p. 93-101, 2020.
DATTA, Jayeeta; KOPCZYŃSKA, Paulina. Effect of kenaf fibre modification on morphology and mechanical properties of thermoplastic polyurethane materials. Industrial Crops and Products, v. 74, p. 566-576, 2015.
EL-SHEKEIL, Yasser Ahmed et al. Effect of alkali treatment on mechanical and thermal properties of Kenaf fiber-reinforced thermoplastic polyurethane composite. Journal of Thermal Analysis and Calorimetry, v. 109, n. 3, p. 1435-1443, 2012.
FIÉVET, Fernand; BRAYNER, Roberta. The polyol process. In: Nanomaterials: a danger or a promise? A chemical and biological perspective. London: Springer London, 2012. p. 1-25.
GIRALDELLI, Mariana Aparecida et al. Propriedade da Fibra de Coco: Uma Revisão Sistemática. UNICIÊNCIAS, v. 24, n. 1, p. 34-38, 2020.
KIM, Sang Jin et al. Potential of a bio-disintegrable polymer blend using alkyl-chain-modified lignin. Fibers and Polymers, v. 16, p. 744-751, 2015.
KURANCHIE, Charles et al. The effect of natural fibre reinforcement on polyurethane composite foams–a review. Scientific African, v. 11, p. e00722, 2021.
ORGANIZAÇÃO DAS NAÇÕES UNIDAS. Transformando Nosso Mundo: A Agenda 2030 para o Desenvolvimento Sustentável. 2015. Disponível em: https://sustainabledevelopment.un.org/post2015/transformingourworld. Acesso em: 23 ago. 2023.
SINGH, Indresh et al. Recent advancement in plant oil derived polyol‐based polyurethane foam for future perspective: a review. European Journal of Lipid Science and Technology, v. 122, n. 3, p. 1900225, 2020.
TANAKA, Ryohei; HIROSE, Shuji; HATAKEYAMA, Hiroshi. Preparation and characterization of polyurethane foams using a palm oil-based polyol. Bioresource Technology, v. 99, n. 9, p. 3810-3816, 2008.
ZIA, Khalid Mahmood et al. Methods for polyurethane and polyurethane composites, recycling and recovery: A review. Reactive and Functional Polymers, v. 67, n. 8, p. 675-692, 2007.