Autores
Rosendo da Rocha, K. (UFRN) ; Chiavone-filho, O. (UFRN) ; Neves Maia de Oliveira, H. (UFRN)
Resumo
Oil spilled at sea is a problem that demands an efficient and economically
feasible response. Another
apparently unrelated issue is the number of polyurethane foams accumulated in
cities and landfills
after their useful life. The present work relates these two problems so one can
be used to mitigate
the other. Post-consumer polyurethane foams were coated with hexadecanoic acid
(HA) and tested for
their ability to absorb different oils. Coated foams (HA-PC) performance was
compared to unaltered
foams (Un-PC). Oil sorption from Un-PC to HA-PC increased 0.39%, 226.88%, and
40.88% in the system
with diesel, lubricant oil S46, and 20W40 engine oil, respectively. Coating with
HA proved to be a
simple and effective surface modification to increase the oil sorption capacity
of post-consumer
foams.
Palavras chaves
oil spill; surface modification; environment
Introdução
Scientists worldwide seek to transform the actual global energy matrix into a
more sustainable one. However, petroleum dependence will still persist for
decades.
During offshore oil exploration, production, and transport, accidents may
happen, generating oil spills at sea (Soares et al, 2020). In this case,
the first intervention is to encircle the oil spilled with containment barriers,
also known as booms. Then, different oil removal methods can be applied (Hoang
and Chau, 2018). In some cases, the oil is set on fire. In others, surfactants
are used to capture the oil. Pumping the surface layer of the water-oil
interface is still commonly applied as an initial oil concentration procedure.
However, a technique that has been drawing attention is the use of hydrophobic
porous materials to capture the oil (Ko et al, 2020).
Polyurethane, for example, is a highly porous material. Although it absorbs both
water and oil, its selectivity for oil can be acquired by simple surface
modifications. This change may promote a surface with both hydrophobic and
oleophilic characteristics.
One of the main sources of polyurethane is mattresses, which are often made from
100% of this polymer. Due to flaws in environmental legislation, it is common to
find post-consumer mattresses irregularly discarded over the cities or even in
sanitary landfills. Since 2014, Brazil has produced more than 1 million m³ of
new polyurethane foam per day, which increases the need for studies on its reuse
and recycling (Grotto et al, 2020).
In this study, post-consumer polyurethane foam obtained from irregular disposal
was modified using a coating technique with hexadecanoic acid (HA). This
modification's purpose was to enhance the affinity for oil over water aiming for
oil capture in seawater. The same modification was made on new polyurethane foam
for comparison. Water and oil sorption tests were carried out and analyzed
quantitively. This work highlights the reduction, recycling, and reuse of post-
consumer polyurethane foams to remove oil spilled in seawater through simple
surface modifications. Thus, two apparently unrelated problems are addressed:
one waste is used to remove another.
Material e métodos
A 100% polyurethane mattress with a density of 18 kg‧cm-3 was
purchased from a national supplier. A post-consumer mattress with the same
characteristics as the new one was obtained from an irregular disposal area.
There was no visible damage or mechanical compaction, but there were
characteristic time-of-use stains likely from urine and sweat as well as dust
and hairs. Samples of both foams were cut into 1cm x 1cm x 1cm cubes and washed
multiple times with distilled water and 70 % (v/v) ethanol. Seawater was
obtained directly from the Atlantic Ocean (5° 52′ 52″ S, 35° 10′ 16″ W) in
Natal, Brazil, and filtered on blue band filter paper to remove suspended
solids. Diesel, lubricating oil S46, and engine oil 20W40 were purchased from a
national fuel chain. Turpentine solvent was purchased at a local supermarket.
Anhydrous ethanol (99%), and HA were purchased from Dinâmica Química
Contemporânea, Brazil. All analytical reagents were used without further
purification.
In a beaker, 200 mL of a 10 mmol.L-1 solution of HA in ethanol was
prepared. The foams cubes were submerged for 48 h in the solution inside a
sealed flask to avoid solvent evaporation. After that, the foams were washed
with 70% (v/v) ethanol and oven-dried at 60°C.
The sorption tests were performed in accordance with ASTM F726-12: Standard Test
Method for Sorbent Performance of Adsorbents. The test for determining the
amount of water/oil sorbed was performed in accordance with ASTM D95-13:
Standard Test Method for Water in Petroleum Products and Bituminous Materials by
Distillation.
The morphology of the new and post-consumer PU foams, modified and unmodified,
was analyzed by Scanning Electron Microscopy (SEM). SEM analyses required
previous gold coating. Chemical elements were semi-quantified by Energy-
Dispersive X-ray Spectroscopy (EDS) (JSM - 6610LV, Jeol, Japan). Hydrophobic and
oleophilic characteristics were evaluated in a Drop Shape Analyzer (DSA 100,
Kruss, Germany).
Resultado e discussão
Figure 1 shows SEM + EDS images for the new (N) and post-consumer (PC)
polyurethane foams unaltered (Un) and after coating
with hexadecanoic acid (HA).
It can be observed that there was no change in the pores' structure after the
chemical modification. There is also no
perceptible difference in structure between the new and post-consumer unchanged
foams, which means there was no deformation
due to the time of use. This is essential to maintain the sorption ability to
fulfill the channels with oil.
EDS analyses identified the presence of carbon, nitrogen, oxygen, and calcium in
all foams evaluated. For the HA-N, in
addition to these elements, traces of magnesium were also identified. The
presence of C, N, and O was already expected since
they are widely found in the repeater structure of the polyurethane polymer.
The presence of hydrogen is also assured. However, due to the limitations of the
technique employed, it was not possible to
quantify light elements, such as hydrogen (atomic mass = 1 u).
There was a significant reduction in the contact angle for the unaltered foams
when oil was used instead of seawater. Un-N and
Un-PC contact angles between seawater drops and their surfaces were 90.1° and
104.4°, respectively, and 77.3° and 82.2°,
respectively, between their surfaces and lubricant oil S46 drops. The HA-N and
HA-PC foams presented a 0° angle for the
sorption of lubricating oil S46. The coated foams immediately absorbed the oil
drops, leaving only entry marks. However, the
seawater drop remained as a spherical drop on the surface of HA-PC due to the
hydrophobic effect acquired. The HA-N and HA-PC
contact angles between their surface and seawater drops were 92.4° and 107.7°,
respectively. Although the HA coating did not
significantly increase hydrophobicity, there was a strong increase in oil
affinity compared to foam without coating. In a
medium containing both seawater and oil, HA-PC may be selective for oil over
water sorption, as theoretically expected.
The seawater-oil multicomponent sorption tests shown in Figure 2 were performed
in three different systems.
In the first system, formed by seawater (92%):(8%) diesel oil (viscosity ~4
cSt), the water sorption ranged from 2.01 ± 0.12
g‧g-1 (Un-N) to 7.26 ± 0.22 g‧g-1 (HA-N) for new foams and
from 1.39 ± 0.02 g‧g-1 (Un-PC) to
2.80 ± 0.26 g‧g-1 (HA-PC) for post-consumer foams. The sorption of
diesel oil ranged from 38.21 ± 1.12 g‧g-1 (Un-N) to 39.19 ± 0.92 g‧g-1 (HA-
N) for new foams and
from 41.18 ± 1.02 g‧g-1 (Un-PC) to
41.34 ± 1.16 g‧g-1 (HA-PC) for post-consumer foams. In a similar
study but with a different coating technique,
Sarup et al (2022) coated new polyurethane foam with textile sludge-
derived biochar + polydimethylsiloxane and obtained
maximum sorption of 26.88 g‧g-1 for diesel.
In the second system, formed by seawater (92%):(8%) lubricating oil S46
(viscosity ~46 cSt), the water sorption ranged from
0.21 ± 0.02 g‧g-1 (Un-N) to 0.79 ± 0.02 g‧g-1 (HA-N) for
new foams and from 0.08 ± 0.01 g‧g-1
(Un-PC) to 0.35 ± 0.06 g‧g-1 (HA-PC) for post-consumer foams. The
sorption of lubricating oil S46 ranged from 5.88
± 0.11 g‧g-1 (Un-N) to 10.59 ± 0.22 g‧g-1 (HA-N) for new
foams and from 3.20 ± 0.02 g‧g-1 (Un-
PC) to 10.46 ± 0.36 g‧g-1 (HA-PC) for post-consumer foams. In a
similar study, Jamsaz and Goharshadi (2020)
evaluated the sorption capacity of hydraulic oil (similar to S46 oil) in new and
unmodified polyurethane foam and obtained
maximum sorption of 4 g‧g-1.
In the third system, formed by sea water (92%):(8%) 20W40 motor oil (viscosity
~120 cSt), the water sorption ranged from 0.08
± 0.01 g‧g-1 (HA-N) to 0.33 ± 0.11 g‧g-1 (Un-N) for new
foams and from 0.01 ± 0.00 g‧g-1 (HA-
PC) to 0.61 ± 0.02 g‧g-1 (Un- PC) for post-consumer foams. The 20W40
motor oil sorption ranged from 2.39 ± 0.12 g‧g-1 (Un-N) to 3.10 ± 0.02 g‧
g-1 (HA-N) for the new foams
and from 1.81 ± 0.02 g‧g-1 (Un-PC) to
2.55 ± 0.03 g‧g-1 (HA-PC) for post-consumer foams.
For post-consumer foams, from Un-PC to HA-PC, seawater sorption increased by
101.44% in the diesel system and 337.50% in the
S46 lubricating oil system. However, it reduced 98.36% in the system with 20W40
engine oil. The sorption of oil from Un-PC to
HA-PC increased 0.39% in the system with diesel, 226.88% in the system with
lubricating oil S46, and 40.88% in the system with
20W40 engine oil.
The results showed that, for a low viscous oil such as diesel, for example,
there was no significant difference (p-value >
0.05) between the foams, whether new or post-consumer, modified or not. This
probably happened because there was no resistance
of the pores to the diesel flow, which could mean that intermolecular forces are
not the most important factor for low
viscosity oils. Zhu et al. (2022) compared the results of gasoline
sorption on new polyurethane foam (16.55 g‧g-1) and polyurethane foam modified with
chitosan and nano-
montmorillonite (25.24 g‧g-1). Gasoline has
an even lower viscosity than diesel (> 1 cSt). These results show that even
without modification, low-viscosity oils are
easily absorbed.
When the oil viscosity was increased, the unmodified foams showed greater
resistance to oil sorption than the HA-coated foams.
This is because HA is a long-chain fatty acid and, although it has the carboxyl
group (able to form hydrogen bonds), the long-chain is formed exclusively from typically dipole-
induced C-H bonds. In this
way, the surface of the polyurethane becomes more
oleophilic and contributes to the sorption, passage, and retention of the sorbed
oil, proving the effectiveness of the
modification.
It is also important to note that post-consumer foams showed statistically
similar results to the new foams, which proves the
possibility of its use for the sorption purpose.
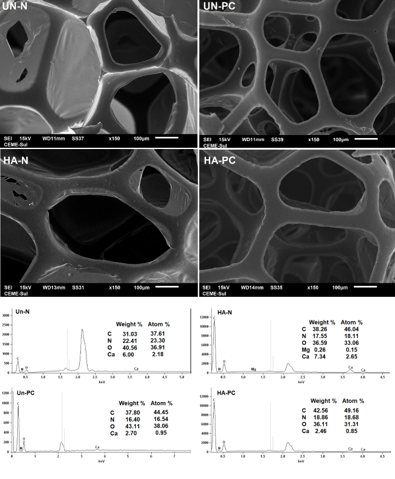
SEM + EDS images for new (N) and post-consumer (PC) polyurethane foams unmodified (Un) and after hexadecenoic acid (HA) coating
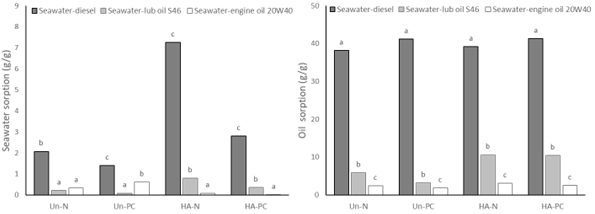
Seawater and oil sorption in the three systems with seawater and diesel or lub oil S46 or engine oil 20W40
Conclusões
Post-consumer polyurethane foams demonstrated similar sorption performances to
new
foams. This showed that, regardless of age or time of use of the foams,
adaptation
for oil sorption is feasible. The sorption of oil from Un-PC to HA-PC increased
0.39% in the system with diesel, 226.88% in the system with lubricating oil S46,
and 40.88% in the system with 20W40 engine oil. Coating with hexadecanoic acid
(HA) proved to be a simple, cheap, and effective surface modification to increase
the oil sorption capacity of post-consumer foams.
Agradecimentos
This work is supported by the Brazilian National Agency of Petroleum, Natural Gas
and Biofuels through the Human Resources Program PRH 44.1.
Referências
A. F726-12, Standard test method for sorbent performance of adsorbents, Annual Book of ASTM Standards, 2012.
A. D95-13, Standard test method for water in petroleum products and bituminous materials by distillation, Annual Book of ASTM Standards, 2013.
GROTTO, A. C.; HEMKEMEIER, M.; ROSSATO, M. V. Sustainability in the use of polyurethane and reuse of shavings. Research, Society and Development, v. 9, n. 1, p. 1-26, 2020.
HOANG, A. T.; CHAU, M. Q. A mini review of using oleophilic skimmers for oil spill recovery. Journal of Mechanical Engineering Research & Developments, v. 41, n. 1, p. 92-96, 2018.
JAMSAZ, A.; GOHARSHADI, E. K. An environmentally friendly superhydrophobic modified polyurethane sponge by seashell for the efficient oil/water separation. Process Safety and Environmental Protection, v. 139, n. 1, p. 297-304, 2020.
KO, T. J.; HWANG, J. H.; Davis, D.; SHAWKAT, M. S.; HAN, S. S.; RODRIGUEZ, K.; OH, K. H.; LEE, W. H.; JUNG Y. Superhydrophobic MoS2-based multifunctional sponge for recovery and detection of spilled oil. Current Applied Physics. v. 5116, n. 1, p. 1-33, 2020.
SARUP, R.; SHARMA, M.; BEHL, K.; AVASTHI, D. K.; KUMAR, P.; OJHA, S.; NIGAM, S.; JOSHI, M. Fabrication of superhydrophobic Polyurethane sponge coated with oil sorbent derived from textile sludge for oily wastewater remediation. Environmental Nanotechnology, Monitoring & Management, (In Press, Journal Pre-proof), 2022.
SOARES, M. O.; TEIXEIRA, C. E. P.; BEZERRA, L. E. A.; PAIVA, S. V.; TAVARES, T. C. L.; GARCIA, T. M.; CAVALCANTE, R. M. Oil spill in South Atlantic (Brazil): Environmental and governmental disaster. Marine Policy, v. 115, n.1, p. 01-07, 2020.
ZHU, G.; WANG, J.; YUAN, X.; YUAN, B. Hydrophobic and fire safe polyurethane foam coated with chitosan and nano-montmorillonite via layer-by-layer assembly for emergency absorption of oil spill. Material letters, v. 316, n. 1, p. 1-4, 2022.