TRATAMENTO DE EFLUENTE GERADO NA PRODUÇÃO DO BIODIESEL ATRAVÉS DA UTILIZAÇÃO DA ZEÓLITA A
ISBN 978-85-85905-25-5
Área
Ambiental
Autores
Lotero, R.P. (UNP) ; Silva, L.B. (UFRN) ; Galvão, L.P.F.C. (UFRN) ; Bezerra, B.G.P. (UFRN)
Resumo
O biodiesel é menos poluente e renovável; no entanto, seu processo convencional de obtenção gera um efluente de difícil degradação natural. Apesar da corrente de fluido ser de difícil tratabilidade, a proveniente da sintetização do biodiesel (que ocorreu na Universidade Potiguar – Nascimento de Castro) apresentou valores de metais presentes menores que os máximos permitidos descritos nas Resoluções do CONAMA nº 357 e 430. Mesmo com os níveis de metais presentes dentro dos parâmetros, o objetivo do trabalho foi tratar o efluente gerado na produção de biodiesel através da utilização da zeólita A e minimizar, ainda mais, tais índices. Como resultado, a quantidade de metais como Fe, Mn e Zn foi reduzida significativamente, mostrando a eficiência da metodologia utilizada.
Palavras chaves
Biodiesel; Efluente; Zeólita A
Introdução
O grande potencial poluidor dos combustíveis fósseis faz com que haja uma busca crescente por fontes alternativas e renováveis de energia. Os biocombustíveis, derivados de matérias-primas renováveis onde os processos de produção são sustentáveis, surgem como alternativa por oferecerem benefícios que incluem características não poluentes, biodegradáveis e que contribuem para a sustentabilidade (CREMONEZ et al, 2015) (LOSSAU et al, 2015) (REIJNDERS, 2006) (PUPPAN, 2002). A utilização da energia proveniente da biomassa é apontada como uma grande opção que pode contribuir para o desenvolvimento sustentável nas áreas ambiental, social e econômica (TREVISANI et al, 2007) (HAMELINCK & FAAIJ, 2006). Como exemplo do emprego da mesma tem-se a utilização do biodiesel, combustível produzido pela reação química entre um óleo vegetal (ou gordura animal) com um álcool, que possui queima limpa, não apresenta toxidade e é considerado um combustível ecologicamente correto (GERPEN, 2005) (LOTERO et al, 2005) (COSTA & OLIVEIRA, 2006). O método de obtenção do biodiesel incentivado pelo governo brasileiro é o de transesterificação, que consiste na reação química de triglicerídeos com álcoois (metanol ou etanol) na presença de um catalisador (ácido, básico ou enzimático), resultando na substituição do grupo éster do glicerol pelo grupo etanol ou metanol (SILVA & FREITAS, 2008). Após a reação de transesterificação, o glicerol é removido dos ésteres metílicos (ou etílicos) por decantação. No entanto, para atender aos critérios de qualidade é necessária a etapa de purificação, para a remoção de qualquer quantidade de resíduo que tenha ficado no biodiesel, para isto é realizada uma lavagem aquosa onde ocorre a remoção de qualquer catalisador remanescente, sabões, sais, metanol e glicerina livre do biodiesel (KNOTHE et al, 2006). Segundo Suehara et al. (2005), utilizando o processo de transesterificação, para cada 100 L de biodiesel produzido, são gerados 20 L de efluente; Kolesárová et al. (2010), e que dependendo do método de lavagem aplicado cerca de 300 L de efluente podem ser gerados para cada 100 L de biodiesel produzidos. De Boni et al. (2007) verificaram que são necessários no mínimo 3 L de água para cada litro de biodiesel produzido, fato comprovado por Granjeiro (2009) que utilizou 3 L de água deionizada ne lavagem de 1 L de biodiesel. Tendo em vista que a demanda atual de biodiesel é atendida pelo processo convencional de transesterificação com catalisador alcalino, o efluente gerado possui alto valor de pH, alto teor de óleo e de sólidos e baixa concentração de nitrogênio. Quando juntos, estes componentes inibem o crescimento da maioria dos micro-organismos, o que dificulta a degradação natural do efluente. Portanto, diante da crescente expansão da produção de biodiesel em plantas industriais que utilizam o processo convencional, verifica-se a necessidade de tratar o efluente gerado durante este processo produtivo (JARUWAT et al, 2010), de forma que adquira características dentro dos padrões de lançamento de efluentes presentes na Resolução CONAMA nº 430 de 13/05/2011, a qual complementa e altera a resolução CONAMA ¬¬¬-357/2005. Atualmente existem diversas pesquisas que podem ser utilizadas para o tratamento do efluente gerado na produção do biodiesel, dentre os métodos destaca-se tratamento por adsorção. Neste trabalho, após a sintetização do biodiesel (que ocorreu em um dos laboratórios de química da Universidade Potiguar – Nascimento de Castro) buscou-se tratar o efluente através da utilização da zeólita A, um material formado por tetraedros de SiO4 e AlO4 conectados por átomos de oxigênio em seus vértices, cuja composição pode ser representada genericamente por Mx/nAlxSiy O2(x+y).wH2O, onde M é um cátion de valência n e (x+y) corresponde ao total de tetraedros na cela unitária (BRECK, 1974). Sua estrutura é microporosa e apresenta canais e cavidades – que variam de uma zeólita para outra, o que permite a mobilidade de íons e propicia seletividade aos processos de troca iônica (GASPARD et al, 1983). Nestes canais e cavidades encontram-se os cátions de compensação, moléculas de água ou outros adsorvatos. Alguns dos cátions típicos encontrados são metais alcalinos (Na+, K+, Rb+, Cs+) e alcalinos terrosos (Mg2+, Ca2+), NH4+, H3O+, TMA+ (tetrametilamônio) e outros cátions nitrogenados, terras raras e metais nobres (DANA & HURLBUT, 1970). O processo de troca iônica relaciona-se diretamente à substituição de cátions intersticiais M por cátions da solução, dependendo basicamente de fatores como natureza das espécies catiônicas (tamanho, carga e grau de hidratação) e sua respectiva concentração, temperatura, espécies aniônicas associadas aos cátions em solução, solvente empregado e característica da zeólita em questão (COLELLA, 1999)(SHERMAN, 1984).
Material e métodos
Na determinação dos metais foi utilizado um ICP-OES (Thermo Fisher Scientific, Bremen, Alemanha), modelo iCAP 6300 Duo, com vista axial e radial, detector simultâneo CID (Charge Injection Device). Argônio comercial com pureza de 99,996% (White Martins-Praxair) foi utilizado para purgar a óptica, geração do plasma, sendo também utilizado como gás de nebulização e auxiliar. No sistema de introdução de amostra foi utilizado um nebulizador Burgener Miramist e câmara de nebulização do tipo ciclônica. Nesse sistema, a amostra era bombeada para o plasma com uma bomba peristáltica acoplada ao equipamento e seu fluxo era controlado pelo programa (iTeva – Thermo Scientific). A tocha utilizada foi de quartzo do tipo desmontável. Os parâmetros instrumentais foram otimizados em função da robustez do plasma para soluções aquosas acidificadas. Foram estes: Potência da fonte de RF, 1150 W; vazão do gás nebulizador, 0,75 L/min; vazão do gás auxiliar, 0,5 L/min; tempo de estabilização, 15 s; comprimentos de onda utilizados: Fe (259,837 nm), Mn (260,569 nm), e Zn (213,856 nm). Uma balança analítica Marte, Shimadzu, modelo AY220, foi utilizada para a pesagem das massas de Zeólita A. foi utilizada uma mesa agitadora orbital (SOLAB) moledo SL – 180/D. Todas as soluções aquosas foram preparadas com água de alta pureza, com resistividade de 18,2 MΩ cm, obtida pelo sistema Elga Purelab Ultra (Elga Labwater, Reino Unido). Para o preparo da curva de calibração, soluções de referência (SpecSol, São Paulo) mono-elementares de 1000 mg L-1 de Fe, Mn e Zn 5 % (v/v) de HNO3, foram utilizados; foi utilizada a zeólita A comercial como material adsorvente. O tratamento do efluente oriundo da produção do biodiesel foi realizado empregando 50 mL da solução em contato com uma massa de 0,30 g da zeólita A comercial. As amostras foram colocadas em erlenmeyers de 150 mL e submetidas a uma agitação em mesa agitadora orbital numa rotação de 200 rpm, em períodos iguais de 4h00, procedimento usado em trabalhos anteriores por (BEZERRA et al, 2019). Ao término de tempo, a amostra foi filtrada recuperando a zeólita A e o líquido foi analisado por ICP-OES. O procedimento foi realizado em duplicatas e o branco foi considerado o do tempo zero, ou seja, o qual não entrou em contato com a peneira molecular.
Resultado e discussão
Na Figura 1 se encontram as concentrações de três metais presentes no efluente
após a síntese do biodiesel. As concentrações iniciais no tempo zero, ou seja,
sem o tratamento são de 146.00 µg L-1 para Fe; 45.00µg L-1 para Mn e 30.00 µg
L-1 para Zn. Após o tratamento com a zeólita A comercial, observa-se que há
uma diminuição significativa da concentração de todos os analitos, os valores
obtidos em triplicatas por ICP-OES são de 25.00 µg L-1 para Fe; 7.00µg L-1
para Mn e 10.00 µg L-1 para Zn.
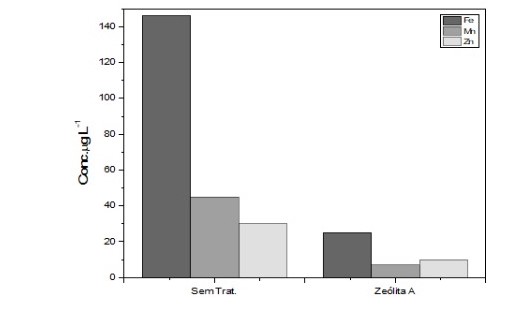
Variações das concentrações dos íons Fe, Mn e Zn no efluente antes e após o tratamento com a Zeólita A por ICP-OES.
Conclusões
O estudo do tratamento de efluentes residuais da produção de biodiesel através da adsorção de metais utilizando o mineral zéolita A comercial como adsorvente foi satisfatória. Conforme os valores obtidos na Figura 1, as concentrações iniciais dos metais presentes no efluente já estavam menores que os valores máximos permitidos estabelecidos pelas Resoluções do CONAMA nº 357 e 430, evidenciando que a síntese do biodiesel está de acordo com padrões ambientais. Após o tratamento, o efluente obteve concentrações ainda menores provando que a zéolita A comercial é um material adsorvente capaz, permitindo rápida e fácil extração dos elementos presentes em matrizes complexas.
Agradecimentos
Referências
BEZERRA, Breno Gustavo P. et al. Cleaning produced water: A study of cation and anion removal using different adsorbents. Journal of Environmental Chemical Engineering, v. 7, n. 2, p. 103006, 2019.
BRECK, D. W.; Zeolite Molecular Sieves, Wiley: New York, 1974
COLELLA, C. Em Natural Microporous Materials in Environmental Technology; Misaelides, P.; Macásek, F.; Pinnavaia, T. J.; Colella, C., eds.; Kluwer Academic Pub.: London, 1999, p. 207.
CONAMA – Conselho Nacional do Meio Ambiente. Disponível em: <http://www2.mma.gov.br/port/conama/legiabre.cfm?codlegi=646>; acesso em 19 de maio de 2019.
COSTA, J. B.; OLIVEIRA, S. M. M. de. Produção de biodiesel. [Curitiba]: Instituto de Tecnologia do Paraná, 2006. Dossiê Técnico elaborado para o Serviço Brasileiro de Respostas Técnicas.
CREMONEZ, P. A.; FEROLDI, M.; FEIDEN, A.; TELEKEN; J. G.; GRIS, D.J.; DIETER, J.; ROSSI, E.; ANTONELLI, J. Current scenario and prospects of use of liquid biofuels in South America. Renewable and Sustainable Energy Reviews 2015, 43, 352. [CrossRef]
DANA, J. D.; HURLBUT Jr., C. S.; Manual de Mineralogia, Ao Livro Técnico S.A.: Rio de Janeiro, 1970.
DE BONI, L. A. B.; GOLDANI, E.; MILCHAREK, C. D.; SANTOS, F. A.; Tchê Química 2007, 4, 41.
GASPARD, M.; NEVEU, A.; MARTIN, G.; Water Res. 1983, 17, 279
GERPEN, J. V.; Fuel Process. Technol. 2005, 86, 1097
GRANJEIRO, R. V. T.; Dissertação de Mestrado, Universidade Federal da Paraíba, Brasil, 2009.
HAMELINCK, C. N.; FAAIJ, A. P. C.; Energy Policy 2006, 34, 3268.
JARUWAT, P.; SANGKORN, K.; HUNSOM, M.; Energy Conversion Manag. 2010, 51, 531.
KNOTHE, G.; VAN GERPEN, J.; KRAHL, J.; RAMOS, L. P.; Manual de Biodiesel, 1a ed., Editora Edgard Blücher: São Paulo, 2006.
KOLESÁROVÁ, N.; HUTNAN, M.; SPAÇKOVÁ, V.; LAZOR, M.; 37th International Conference of SSCHE, Tatranski Matliare, Slovakia, 2010.
LOSSAU, S.; FISCHER, G.; TRAMBEREND, S.; VELTHUIZEN, H.; KLEINSCHMIT, B.; SCHOMÄCKER, R. Brazil's current and future land balances: Is there residual land for bioenergy production? Biomass and Bioenergy 2015, 81, 452.
LOTERO, E.; LIU, Y.; LOPEZ, D. E.; SUWANNAKARN, K.; BRUCE, D. A.; GOODWIN, J. G.; Ind. Eng. Chem. Res., 2005, 44, 5353;
PALOMINO-ROMERO, J. A.; LEITE, O. M.; BARRIOS EGUILUZ, K. I.; SALAZARBANDA, G. R.; SILVA, D. P.; CAVALCANTI, E. B. Tratamentos dos efluentes gerados na produção de biodiesel. Química Nova, v. 35, p. 367-378, 2012.
PUPPAN, D. Environmental evaluation of biofuels. Periodica Polytechnica, v.10, p. 95-116, 2002.
REIJNDERS, L. Conditions for the sustainability of biomass based fuel use. Energy Policy. v. 34, p.863–876, 2006.
RUBACH, S.; SAUR, I. F.; Filt. Sep.1997, 34, 877.
SHERMAN, J. D. Em Zeolites: Science and Technology; NATO Advanced Study Institute Series, Applied Sciences, Ser. E, N°. 80, Ribeiro, F. R, ed.; Martinus Nijhoff Publishers: Boston, 1984, p. 583.
SILVA, P. R. F. da; FREITAS, T. F. S.; Ciência Rural 2008, 38, 843.
SINOTI, A. L. L.; SOUZA, M. A. A.; Anais do 23° Congresso Brasileiro de Engenharia Sanitária e Ambiental, Campo Grande, Brasil, 2007.
SUEHARA, K.; KAWAMOTO, Y.; FUJII, E.; KOHDA, J.; NAKANO, Y.; YANO, T.; J. Biosci. Bioeng. 2005, 100, 437.
TREVISANI, L.; FABBRI, M.; NEGRINI, F.; RIBANI,P. L.; Energy Convers. Manage. 2007, 48, 146;