Avaliação da influência do tipo de compactação na evolução microestrutural e propriedades mecânicas de cerâmicas porosas de alta alumina.
ISBN 978-85-85905-23-1
Área
Materiais
Autores
Gusmão, E. (UNIFESSPA) ; Braga Pedrosa, E.P. (UNIFESSPA) ; Nazar de Oliveira, D. (UNIFESSPA) ; Souza, A.D. (UNIFESSPA)
Resumo
Cerâmicas porosas desperta interesse crescente devido à diversidade de áreas em que podem ser aplicadas, por exemplo, catálise, filtros e isolamento térmico em revestimentos de fornos. Apesar do bom desempenho, cerâmicas porosas apresentam baixa resistência termomecânica e redução de porosidade causada pelos fenômenos de sinterização e crescimento de grãos que se intensificam acima de 1100 °C, o que representa uma grande limitação de uso em isolamento térmico. Entretanto, combinando-se adequadamente as matérias- primas e as técnicas de processamento, tais como o método de compactação, esses aspectos negativos podem ser minimizados. Neste trabalho, busca-se avaliar a influência do tipo de compactação na evolução microestrutural e propriedades mecânicas de cerâmicas porosas de alta alumina.
Palavras chaves
Cerâmica; Porosa; Alumina
Introdução
Cerâmicas porosas desperta interesse devido à diversidade de áreas que podem ser aplicadas, como suportes catalíticos, filtros para combustíveis e isolamento térmico (CORONAS, 1994). Para aplicações como isolantes térmicos em altas temperaturas, seu uso é particularmente importante, pois combina alta refratariedade da fase densa com baixa condutividade térmica da fase porosa. Apesar desse bom desempenho, tal sistema apresenta baixa resistência termomecânica, devido à elevada porosidade, além da redução de porosidade causada pelos fenômenos de sinterização e crescimento de grãos que se intensificam acima de 1100 °C (KINGERY, 1976). Diversos trabalhos demonstram que combinando-se adequadamente as matérias- primas e as técnicas de processamento, como o método de compactação, esses aspectos negativos podem ser minimizados (SALOMÃO, 2011). Com base na literatura, a resistência termomecânica pode ser melhorada através do aumento da eficiência de empacotamento das partículas, do aprimoramento dos métodos de processamento para diminuir a introdução de defeitos ou ainda pelo uso de aditivos para controlar a sinterização (OSTROWSKI, 1999). Já a manutenção da porosidade em altas temperaturas pode ser conseguida com o aumento da fração inicial de poros no material verde, com rampas de aquecimento e sinterização controladas ou ainda com a introdução de compostos que minimizem o crescimento de grão e a densificação como, por exemplo, espinélio, mulita ou hexaluminato de cálcio (BRAULIO, 2009). Neste trabalho, busca-se avaliar influência do tipo de compactação na evolução microestrutural e propriedades mecânicas de cerâmicas porosas de alumina/hidróxido de alumínio compactadas por meio de prensagem uniaxial e moldagem, usando alumina hidratável como ligante em ambos os métodos.
Material e métodos
Preparação das amostras moldadas Suspensões aquosas contendo 45% vol. de alumina calcinada e 45% vol. de hidróxido de alumínio foram homogeneizadas em um moinho de esferas por 2 h. Em seguida, 10 % vol. do ligante hidráulico alumina hidratável foi adicionado e a suspensão homogeneizada em misturador mecânico por 3 minutos a 500 rpm. As suspensões foram moldadas na forma de cilindros (20 mm x 40 mm), e permaneceram em ambiente de elevada umidade por 24 h a 50ºC e, em seguida, em ambiente ventilado por 24 h a 50ºC 1ºC. Após a desmoldagem, as amostras foram secas a 120ºC por 24 horas. Preparação das amostras prensadas Amostras com a mesma composição foram homogeneizadas em moinhos de esferas com álcool isopropílico e esferas de Zircônia durante 30 minutos. Em seguida, a suspensão foi seca em estufa para posteriormente ser compactada na forma de barras de 6 x 20 x 60 mm sob compressão uniaxial de 40 Mpa. Todas as amostras (prensadas e moldadas) foram tratadas termicamente de 1100 a 1500°C (taxa de 5°C/min, patamar de 2°C horas a 400°C e 3 horas na temperatura final. Finalmente, as amostras verdes e após tratamentos térmicos foram caracterizadas em relação a porosidade total geométrica (PTG, %), através do método geométrico, o módulo elástico (E) foi medido pela técnica de ressonância de barras (equipamento Sonelastic, ATCP, Brasil) de acordo com a norma ASTM C 1198-91 e a microestrutura foi avaliada por meio de microscopia eletrônica de varredura nas superfícies de fratura das amostras, no equipamento JEOL JSM-7500F.
Resultado e discussão
A Figura 1 mostra a porosidade total e
módulo elástico das amostras
compactadas por meio de prensagem
uniaxial ou moldagem, contendo 45% de
Al2O3, 45% de Al(OH)3 e 10% de ligante
hidráulico em função da temperatura
de sinterização. Observa-se na Figura 1
que as amostras verdes, compactadas
por meio de prensagem ou moldagem
apresentaram um nível de porosidade
total
próximo 35% (Figura 1A), enquanto o
módulo elástico ficou em torno de 10 GPa
(Figura 2B). Com o aumento da
temperatura para 1100 °C houve um
aumento
significativo do nível de porosidade
total ao mesmo tempo que ocorreu uma
diminuição da resistência mecânica. Esse
efeito está associado a
decomposição do hidróxido de alumínio e
a formação das aluminas de transição
com alta concentração de defeitos (poros
e trincas) em suas superfícies.
Além disso, observa-se também que para
ambos os casos os níveis de
porosidade total alcançados, bem como a
resistência mecânica foram os
mesmos, já que o teor de hidróxido de
alumínio é igual.
Em 1300 °C a porosidade total começou a
diminuir ao mesmo em que a
resistência mecânica começou a aumentar.
Isso ocorre devido o início do
processo de sinterização, onde vai
ocorrer o empescoçamento das partículas.
Com o aumento da temperatura para 1500
°C as amostras apresentaram uma
diminuição nos níveis de porosidade
total que está associado à sinterização
da matriz e ao desaparecimento da
mesoporosidade localizada nas
superfícies
das partículas de hidróxido de alumínio
(Figura 1A). Observa-se também que
com a diminuição da porosidade as
amostras tornaram-se mais rígidas
apresentando níveis de resistência
mecânica maiores, em torno de 20 GPa.
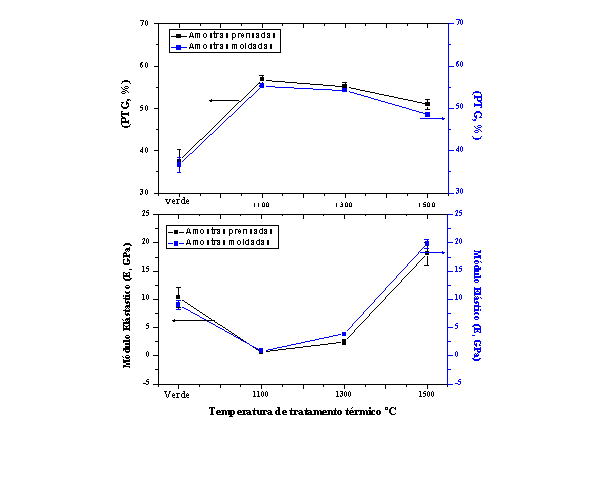
A) PTG (%) e B) E (GPa) de amostras com 45% de Al2O3, 45% de Al(OH)3 e 10% de ligante hidráulico, prensadas ou moldadas em função da T de sinterização
Conclusões
Com base nos resultados obtidos, pode-se observar que o método de compactação (prensagem ou moldagem) não influenciou significativamente na geração de porosidade total e resistência mecânica das amostras verdes e sinterizadas em 1100 °C, 1300 °C e 1500° C com composição de 45% de Al2O3, 45% de Al(OH)3 e 10% de ligante hidráulico.
Agradecimentos
À Fundação de amparo a pesquisa do Pará (Fapespa) pelo apoio financeiro e ao grupo de pesquisa Soluções integradas em manufatura de materiais cerâmicos (Simmac/EESC/U
Referências
BRAULIO, M.A.L.; (2009). From macro to nanomagnesia: designing the in situ spinel expansion. Journal of the American Ceramic Society, n. 91, v. 9, p. 3090-3093.
CORONAS, J.; et al. (1994). Methane oxidative coupling using porous ceramic membrane reactors. Chemistry Engineer Sciety, v. 49, n. 12, p. 2005-2013.
KINGERY, W. D.; et al. Introduction to ceramics. 2ª ed. New York: Wiley Interscience, 1976. p. 788-1016.
OSTROWSKI, T.; et al. (1999). Evolution of Mechanical properties of porous alumina during free sintering and hot pressing. Journal of the American Ceramic Society, v. 82, n.11, p. 3080-3086.
SALOMÃO, R.; et al. (2011). Porous alumina-spinel ceramics for high temperature applications. Ceramics international, v. 37, n. 328, p. 1393-1399.